Métallurgie générale/Les métaux
Résumé
[modifier | modifier le wikicode]Nous étudions ici les principaux métaux et alliages, leurs propriétés, leurs applications. Nous nous intéressons aux métaux sous « forme métallique » — à structure cristalline, sous forme réduite — et non pas sous forme oxydée (par exemple pigments ou céramiques d'oxydes métalliques, minerais), dans des molécules (par exemple fer dans l'hémoglobine) ni sous forme d'éléments d'alliage (par exemple molybdène dans l'acier).
Introduction
[modifier | modifier le wikicode]Historiquement, les métaux et alliages ont été utilisés pour leur facilité à être façonnés — moulage, martelage — et leur dureté — outils, armes —, parfois pour leur brillance — bijoux, miroirs —, voir Introduction à la science des matériaux > Histoire de la science des matériaux > Préhistoire. Leur utilisation s'est lentement développée jusqu'à la révolution industrielle, qui a vu leur production et leur utilisation croître de manière exponentielle : structures (poutrelles), mécanismes, électricité…
De nos jours, de nombreux autres matériaux sont utilisés pour ces applications : céramiques, polymères, matériaux composites, mais les métaux gardent un rôle important.
Propriétés des métaux purs
[modifier | modifier le wikicode]Par « métal pur », nous entendons « cristal métallique composé d'un seul élément ». Les métaux sont rarement utilisés « réellement » purs, pour deux raisons :
- ils contiennent des impuretés provenant des minerais d'origine ou bien introduits par le procédé d'élaboration ;
- les alliages ont souvent des propriétés plus intéressantes.
On élabore parfois des métaux ultra-purs, à des coûts importants, pour des applications spécifiques : recherche scientifique, électronique.
Bien que les propriétés des métaux purs ne correspondent pas aux matériaux réellement utilisés, en particulier la résistivité électrique, elles s'en approchent souvent, et permettent en tous cas de comprendre le choix des matériaux.
Métal | Z | M g/mol |
d g/cm3 |
Tf °C |
Te °C |
λ W/(m⋅K) |
Lf kJ/kg |
Lv kJ/kg |
Cp J/(kg⋅K) |
α 10-6 K-1 |
ρe 10-9 Ω⋅m |
---|---|---|---|---|---|---|---|---|---|---|---|
Aluminium (Al) | 13 | 27 | 2,70 | 660 | 2 519 | 237 | 335 | 9492 | 900 | 22,38 | 26,5 |
Argent (Ag) | 47 | 108 | 10,5 | 961,8 | 2 162 | 429 | 103 | 2 163 | 232 | 18,27 | 15,9 |
Chrome (Cr) | 24 | 52 | 7,14 | 1 857 | 2 672 | 93,7 | 134 | 450 | 8,11 | 129 | |
Cuivre (Cu) | 29 | 64 | 8,92 | 1 084 | 2 567 | 401 | 174 | 4 645 | 395 | 16,7 | 16,8 |
Étain (Sn) | 50 | 119 | 7,31 | 232 | 2 602 | 66,6 | 59,9 | 2 599 | 228 | 20,9 | 109 |
Fer (Fe) | 26 | 56 | 7,987 | 1 535 | 2 750 | 80,2 | 207 | 6362 | 460 | 11,7 | 101 |
Graphite (C) | 6 | 12 | 2,27 | 3 527 | 4 027 | 129 | 0,8 | 16 393 | |||
Magnésium (Mg) | 12 | 24 | 1,74 | 650 | 1 090 | 156 | 301 | 1 825 | 24,9 | 44,2 | |
Nickel (Ni) | 28 | 59 | 8,91 | 1 455 | 2 913 | 90,7 | 306 | 440 | 12,5 | 69,9 | |
Or (Au) | 79 | 197 | 19,3 | 1 064 | 2 856 | 317 | 128 | 14,2 | 22,1 | ||
Platine (Pt) | 78 | 195 | 21,09 | 1 768 | 3 825 | 71,6 | 114 | 130 | 8,87 | 103,5 | |
Plomb (Pb) | 82 | 207 | 11,34 | 328 | 1 749 | 35,3 | 22,9 | 921 | 129 | 27,26 | 207,9 |
Titane (Ti) | 22 | 48 | 4,51 | 1 668 | 3 287 | 21,9 | 437 | 9000 | 520 | 8,6 | 427,4 |
Tungstène (W) | 74 | 184 | 19,3 | 3 422 | 5 555 | 174 | 192 | 4020 | 130 | 4,5 | 112,4 |
Zinc (Zn) | 30 | 65 | 7,14 | 420 | 907 | 116 | 118 | 390 | 29 | 60,2 |
légende :
- Z : numéro atomique ;
- M : masse molaire atomique ;
- d : densité à 20 °C ;
- Tf : point de fusion ;
- Te : point d’ébullition ;
- λ : conductivité thermique ;
- Lf : chaleur latente de fusion ;
- Lv : chaleur latente de vaporisation ;
- Cp : chaleur massique à 20 °C ;
- α : coefficient de dilatation linéaire ;
- ρe : résistivité.
Principaux alliages
[modifier | modifier le wikicode]Les premiers alliages ont été obtenus du fait que le minerai extrait du sol n’est pas pur. Dans la métallurgie moderne, on cherche au contraire à purifier les métaux, puis à les mélanger dans des proportions définies pour avoir un alliage.
Les alliages les plus connus sont :
- alliages d'aluminium :
- duralumin ou AU4G : aluminium, cuivre (3,5 % en masse), manganèse et magnésium (0,4 % chacun), maintenant appelé « 2017 » (vingt dix-sept),
- alpax : aluminium, silicium (12 % en masse) ;
- alliages de cuivre :
- bronze : cuivre (minimum 60 % en masse), étain,
- laiton : cuivre (minimum 60 % en masse), zinc,
- maillechort : cuivre, zinc (env. 20 % en masse) et nickel (15 à 20 %) ;
- alliages ferreux :
- acier : fer + carbone avec moins de 2 % en masse de C (mais plus de 0,008 %) ; possibilité d'ajouter de nombreux éléments (essentiellement chrome, nickel, molybdène) pour avoir un durcissement ou une résistance à la corrosion,
- fonte : fer + carbone avec plus de 2 % en masse de C (6,67 % maximum) ; c’est le premier produit de transformation du minerai, il est utilisé tel quel, ou bien est affiné pour devenir de l'acier ;
- alliages de nickel :
- nickel-chrome : chrome (env. 20 % en masse),
- super-alliages « Inconels[2] » : ajouts de chrome et de fer ;
- zamak : alliage de zinc (95 % en masse), aluminium (4 %), magnésium et cuivre.
Principales applications
[modifier | modifier le wikicode]- Aluminium et ses alliages.
- Avantages : légèreté (faible densité), résistance à la corrosion ;
- inconvénients : impact environnemental (la réduction consomme énormément d'électricité et utilise de la soude, minerai en relativement faible disponibilité), mauvaise tenue en température, prix ;
- utilisation : pour structures légères (menuiserie alu), aviation.
- Argent, or, alliage or-argent
- Avantages : grande malléabilité et ductilité, résistance à la corrosion ;
- inconvénients : faible résistance mécanique, prix, impact environnemental (rejets de mercure de l'orpaillage sauvage, faible disponibilité) ;
- utilisation : joaillerie, conducteur d'électricité (câble de hifi ; pour l'or : électronique ; pour l’argent : contacteurs, encres et pâtes conductrices), monnaie, dorure ou argenture ; pour l’argent : brasure, miroirs.
- Chrome
- inconvénients : rejets toxiques (chrome VI)
- utilisation : pour recouvrir les pièces d'acier (acier chromé, chromage dur) : esthétique et résistance à la corrosion.
- Cuivre, laiton, bronze
- Avantages : faciles à fabriquer (basses températures de fusion), résistant à la corrosion (vert de gris),
- utilisation : inconvénients : prix.
Cuivre :
- Avantages : bonne conductivité électrique et thermique, malléable et ductile (cuivre pur), eutectique avec le phosphore, l'étain et l’argent (brasure) ;
- utilisation : câbles électriques (pur à 99,999 %), échangeurs de chaleur, tuyauterie sanitaire, casseroles (obsolète).
Bronze (cuivre + étain) :
- Avantages : faibles coefficients de frottement, résistance usure, plus dur que le cuivre ;
- utilisation : pièces mécaniques de frottement (coussinets pour palier lisse[3]), statues, cloches, toitures (obsolète), premier métal utilisé pour les armes et les outils à la préhistoire.
Laiton (cuivre + zinc)
- Avantages : plus dur que le cuivre, facile à usiner ;
- inconvénient : relativement fragile ;
- utilisation : éléments de décoration, instruments de précision, robinetterie, poignées de porte, plaques de cabinet (avocat, médecin, …), filigranes (inclusions dans le papier), douilles de munition.
- Étain
- Avantages : faible température de fusion, ductile et malléable ;
- inconvénients : faible tenue mécanique ;
- utilisation : pour fabrication de petites pièces moulées, brasure (brasage tendre[4] en plomberie, électronique), étamage (pour contacts électriques), vaisselle et décoration.
- Fer, aciers, fontes
- Avantages : abondant, bon marché, résistance mécanique, propriétés magnétiques ;
- inconvénients : sensible à la corrosion (rouille) ;
- utilisation : éléments de structure, pièces mécaniques.
- Graphite
- Avantage : très bonne tenue en température, s'usine facilement ;
- inconvénients : brule, fragile ;
- utilisation : résistances de fours industriels, électrodes pour four à arc (acier électrique), électroérosion, moteurs électriques (balais ou « charbons ») et réactions chimiques, lubrifiant solide, dessin (fusain, crayon à papier), ralentisseur de neutrons (modérateur de réacteur nucléaire), composant de matériaux composites, absorbeur et filtre (charbon actif ou activé).
- Magnésium
- Avantage : léger ;
- inconvénient : brûle ;
- utilisation : mèches pour aluminothermie (procédé de soudure), flash pour photographie (obsolète), pièces légères (aéronautique, automobile, appareils portables).
- Nickel
- Avantages : résiste à la corrosion, réfractaire, propriétés magnétiques ;
- inconvénients : cher, lourd, possibilité d'allergie, de cancers (inhalation) ;
- utilisations : pièces de monnaie (francs français), turboréacteurs, chaudières et nucléaire (superalliages à base nickel Inconels), alliages fer-nickel (invar : faible coefficient de dilatation thermique), alliages cuivre-nickel (cupronickels : bonne résistance à la corrosion marine, soudable), cathodes d'accumulateurs (batteries cadmium-nickel, nickel-hydrures de métal).
Nickel-chrome, ou nichrome (80 % de nickel, 20 % de chrome) :
- Avantages : résiste à la corrosion, réfractaire ;
- inconvénients : cher, lourd, possibilité d'allergie, de cancers (inhalation) ;
- utilisations : couronnes et inlay-cores dentaires, résistances chauffantes, systèmes d'allumage pyrotechniques.
Superalliages « Inconels » :
- Avantages : résiste à la corrosion, ductile, grande plage de températures (-20 à 800 °C selon les alliages) ;
- inconvénients : cher, lourd, possibilité d'allergie, de cancers (inhalation) ;
- utilisations : chaudières, cuves de centrales nucléaires.
- Platine
- Avantages : résistant à la corrosion, propriétés magnétiques ;
- inconvénients : prix ;
- utilisation : étalon mètre (obsolète), thermocouples (mesure de température), catalyseurs dans l’industrie chimique, creusets, alliage nickel-osmium (implants médicaux), filament de briquet à alcool.
- Plomb
- Avantages : facile à fondre, à mettre en forme ;
- inconvénients : lourd, toxique (saturnisme) ;
- utilisations : fusibles, tuyauterie (obsolète), fonderie de figurine (obsolète), scellées, munitions.
- Titane
- Avantages : léger, bonne résistance mécanique, bonne résistance à la corrosion, résistance à l'abrasion ;
- inconvénients : prix ;
- utilisations : objets légers (cadres de vélo haut de gamme), aéronautique, aérospatiale, implants dentaires, prothèses, tubes de forage pétrolier.
- Tungstène
- Avantages : dur, haute température de fusion ;
- inconvénient : lourd ;
- utilisation : billes de stylographes, filaments d'ampoules à incandescence (bientôt obsolète), armes (DIME : dense inert metal explosive), collage de verre sur métal, électrode de soudure (procédé TIG : tungsten inert gas), contact de disjoncteurs à haute tension (résiste à la chaleur de l'arc électrique).
- Zinc
- Avantage : facile à fondre, à mettre en forme ;
- inconvénients : ;
- utilisations : pour protéger l'acier contre la corrosion (anode sacrificielle, galvanisation), étanchéité des toitures, gouttières, zamak (alliage de zinc, d'aluminium et de magnésium, pour pièces moulées).
Fabrication et mise en œuvre
[modifier | modifier le wikicode]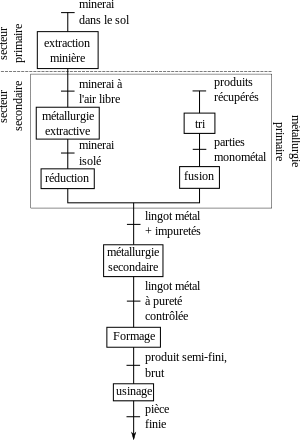
Le processus métallurgique occupe essentiellement le secteur secondaire (transformation) de l'économie, la part du secteur primaire est réduite à l'extraction minière.
On distingue :
- la métallurgie primaire, qui donne le premier produit que l’on peut qualifier de « métal » ;
- la métallurgie secondaire, qui affine le métal, le purifie et lui donne la composition chimique compatible avec les propriétés attendues ;
- le formage, qui donne le brut, c'est-à-dire le produit semi-fini : tôle, barre, tube, profilé, pièce moulée ; c’est le domaine de la chaudronnerie ;
- l'usinage, qui, par enlèvement de matière, donne une forme précise à la pièce.
Métallurgie primaire
[modifier | modifier le wikicode]Comme indiqué précédemment, la plupart des métaux sont présents naturellement à l'état oxydé, principalement sous forme d'oxydes ou de sulfures, sous forme de minerais (roches).
La métallurgie primaire consiste, après récupération du minerai (extraction minière, en carrière), à séparer les différentes composantes de la roche et à réduire le minerai, c'est-à-dire à désoxyder le métal.
La séparation des phases, ou extraction, peut se faire :
- en utilisant une différence de densité, de flottabilité : décantation, centrifugation, filtration, flottaison ;
- en dissolvant une des phases dans une solution aqueuse, c’est la lixiviation :
- lixiviation par un acide (acide sulfurique pour le minerai de cuivre),
- lixiviation par une base (soude pour le minerai d'aluminium) ;
- réaction avec un produit solide contenant de la silice, qui va produire un liquide appelé laitier (pour le minerai de nickel) ;
- en le gazéifiant, c'est-à-dire en le faisant réagir l'oxyde de métal pour le transformer en gaz (réaction du minerai de titane avec du dichlore), puis en le séparant par distillation.
Une fois séparé des autres parties de la roche, l'oxyde métallique peut être réduit :
- par le monoxyde de carbone produit par la combustion de charbon (fer, cuivre) ;
- par le dihydrogène (nickel) ;
- par électrolyse — passage d'un courant électrique dans un liquide — (aluminium).
On parle de pyrométallurgie lorsque l’on utilise la chaleur, d'hydrométallurgie lorsque l’on utilise une solution aqueuse, d'électrométallurgie lorsque l’on utilise le courant électrique.
Métallurgie secondaire
[modifier | modifier le wikicode]La métallurgie secondaire concerne les opérations de purification du métal obtenu : dégazage, élimination des impuretés. Parmi les techniques utilisées :
- mise sous vide du métal en fusion, pour en faire sortir les gaz ;
- addition de produits pour piéger les impuretés dans une phase de densité différente que l’on peut éliminer facilement (laitier flottant sur le métal en fusion) ;
- bullage d'air ou de dioxygène pur (puddlage) pour oxyder certaines impuretés et les piéger dans du laitier.
Formage
[modifier | modifier le wikicode]Les cinq principales opérations de formage sont la coulée en moule, le laminage, l'extrusion, l'estampage et la métallurgie des poudres.
La coulée en moule, ou fonderie, permet de fabriquer des pièces ayant leur forme finale quasiment définitive. Cela permet d’utiliser le minimum de matière lorsque les formes sont complexes. Pour les grandes séries, on peut utiliser des moules permanents métalliques (moulage gravitaire, moulage par injection lorsque l’on « pousse » le métal en fusion dans la moule, moulage par centrifugation lorsque l’on fait tourner le moule pour répartir le métal sur la circonférence). Pour les petites séries, on utilise des moules à usage unique fabriqués par empreinte d'un modèle dans un matériau malléable (moulage en sable, moulage à la cire perdue). Les pièces moulées peuvent présenter des zones creuses grâce à la mise en place de noyaux. Dans le cas des moules métalliques, les noyaux peuvent être mis en place et enlevés de manière automatique, on parle de « moules à tiroirs ».
Le refroidissement provoque un retrait la pièce démoulée à un volume plus petit que le moule. Par ailleurs, la surface peut présenter des creux ou « retassures ». Par ailleurs, l'état de surface est en général rugueux. Les surfaces fonctionnelles, c'est-à-dire devant être en contact avec d'autres pièces, doivent être usinées ; le moule doit prévoir des sur-épaisseurs à ces endroits.
Par ailleurs, la technique impose des contraintes quant à la forme des pièces produites. Pour des raisons d'adhérence, on ne peut pas avoir de surface parallèle au sens du démoulage, les faces doivent être inclinées, ce que l’on nomme la « dépouille ». Les pièces prismatiques ont donc une forme globalement trapézoïdale. On ne peut pas non plus avoir d'arête vive, on a donc des arrondis ou « congés ».
Enfin, la déformation lors du refroidissement peut imposer la présence de zones de renfort ou « nervures ».




Le laminage consiste à écraser le métal entre des rouleaux afin de l'allonger, pour lui donner soit une forme plate, on parle de tôle, soit une forme allongée : on parle de manière générale de fer, de barre lorsque le profil est simple (rond, carré), et de profilé lorsqu’il est plus complexe. Pour les petites séries de tôles, on coule l'acier en lingots, puis on lamine le lingot avec un laminoir réversible : le lingot fait des allers-retours et l’on réduit la hauteur entre les rouleaux entre chaque passage. Pour la fabrication de moyenne et grande série, on des trains de laminoirs : les laminoirs se suivent et ont une distance fixe entre rouleaux. Pour les moyennes séries, on coule des lingots, puis les lingots sont laminés dans un train de laminoirs dégrossisseur pour donner des produits semi-finis :
- bloom (un bloom) pour les produits longs, qui sont ensuite laminés en poutres, rails, profilés ;
- brame (une brame) pour les produits plats, qui sont ensuite laminés en tôles.
Pour les grandes séries, on pratique la coulée continue : la coulée d'acier est guidée et refroidie, puis laminée dans la foulée. Dans le cas des tôles minces, le laminage en continu permet de présenter le produit sous la forme de bobines ou coils.
L'extrusion consiste à pousser ou tirer la matière à travers un trou qui va donner la forme de la section. Cela permet d'obtenir une barre ou un tube.
L'estampage consiste à frapper (forger) le métal pour lui faire prendre la forme d'un moule. Comme la coulée, cette technique permet de réaliser des formes complexes avec un minimum de matière.
Le laminage, l'extrusion et l'estampage peuvent se faire à chaud ou à froid, selon l'épaisseur de la pièce à obtenir et les propriétés du métal. Ils produisent un durcissement par écrouissage.
La métallurgie des poudres consiste à presser de la poudre métallique dans un moule puis à la chauffer pour souder les grains (frittage). L'opération est plus complexe, puisqu’il faut d’abord avoir de la poudre métallique ; en revanche, on ne passe pas par une phase de fusion, ce qui permet de mieux maîtriser la forme obtenue (voir Introduction à la science des matériaux > Diagrammes binaires > Frittage).
La difficulté des opérations tiennent aux propriétés des métaux : température de fusion (moulage, déformation à chaud), fluidité (moulage) et limite élastique (déformation à froid ou à chaud). On peut mesurer cela par l'énergie nécessaire pour effectuer une opération ; il faut bien sûr ramener cela à la quantité de métal nécessaire, donc aux performances intrinsèque du matériau (limite élastique, conductibilité, …).
Métal | Moulage | Laminage, estampage |
Métallurgie des poudres |
---|---|---|---|
Aluminium et alliages | 2,9 à 3,6 | 5,5 à 7,8 | 18,4 à 22,9 |
Cuivre pur et alliages | 2,4 à 3 | 4,8 à 6,3 | 20,7 à 25,3 |
Acier | 2,9 à 3,7 | 5,3 à 8 | 23,7 à 30 |
Fonte | 2,8 à 3,4 | 5,8 à 7 | 22,4 à 27,9 |
Alliage de magnésium | 2,9 à 3,6 | 6 à 8,8 | 18,2 à 22,3 |
Nickel pur et alliages | 2,8 à 3,5 | 5,7 à 7,7 | 24,1 à 29,5 |
Titane pur et alliages | 3,3 à 4,4 | 6,4 à 10,4 | 25 à 31,2 |
Zinc et alliages | 2,2 à 2,6 | 5,2 à 6,3 | 17,5 à 21,4 |
Chaudronnerie
[modifier | modifier le wikicode]La chaudronnerie (fabrication) est le travail du métal sans enlèvement de matière. Il s'agit essentiellement de techniques de découpe (cisaille, oxycoupage), formage (pliage et roulage de tôles, cintrage de tubes) et de soudage.
Il existe plusieurs modes d'assemblage par métal fondu, en fonction du métal d'apport et du procédé de chauffage :
- le brasage : on utilise un métal d'apport ayant une température de fusion inférieure au métal de base (métal des pièces à souder) ; le métal fondu est posé sur le métal chauffé et pénètre entre les pièces par capillarité ;
- brasage tendre (soldering) : on utilise un métal ayant une température de fusion inférieurs à 450 °C, typiquement de l'étain ou de l'argent, le brasage tendre a une faible tenue mécanique et en température,
- brasage fort (brazing) : le métal d'apport a une température de fusion supérieure à 450 °C, typiquement un alliage de cuivre ;
- le soudobrasage (braze welding) : similaire au brasage fort, mais le métal fondu ne pénètre pas par capillarité, il est déposé dans le joint avant chauffage ;
- le soudage : le métal d'apport a une température de fusion similaire au métal de base, il y a donc une fusion des pièces au niveau du cordon de soudure (zone fondue).
Les termes brasure et soudure désignent le résultat alors que les termes soudage et brasage désignent l'opération.
Le soudage donne un assemblage ayant une résistance similaire aux pièces assemblées elles-mêmes. Il demande cependant un chauffage important (typiquement plus de 1 000 °C) et provoque également une déformation importante due au retrait lors de la solidification de la zone fondue. Pour limiter cet effet, on effectue un pointage : on fait des petits points de soudure le long du futur cordon pour tenir les pièces. Pour souder des pièces épaisses bout à bout, on chanfreine les pièces : on taille l'extrémité en biseau, ainsi, lors du soudage, une surface conséquente du métal de base est chauffé et fond ce qui permet de réaliser la zone fondue. En absence de chanfrein, on ne réalise qu'un « collage », similaire à une brasure, le métal de base ne participe pas au cordon de soudure.
Le soudobrasage et le brasage permettent de chauffer moins, de moins déformer l'assemblage, et d'assembler des métaux différents. Cependant, le résultat est moins résistant que la soudure.
Pour le brasage, on chauffe en général avec une flamme (chalumeau oxyacétylénique) ; pour le brasage tendre, on peut utiliser une résistance chauffante (fer à souder pour l'électronique). Pour la soudure, on peut utiliser une flamme ou un arc électrique (soudure à l'arc), et dans certains cas un laser. Il peut être nécessaire de protéger la zone fondue par un gaz inerte (argon) pour éviter l'oxydation du métal, en particulier pour l'aluminium et les aciers inoxydables.
Les techniques de chaudronnerie permettent de fabriquer des assemblages avec des tolérances dimensionnelles de l’ordre du millimètre, mais un travail très soigné permet de faire de la chaudronnerie de précision.
-
Pliage d'une tôle
-
Roulage d'une tôle
-
Soudure à l'arc
-
Soudure à l'oxy-acétylène
-
Canalisations en cuivre brasées (plomberie)
Usinage
[modifier | modifier le wikicode]


L'usinage consiste à enlever de la matière avec un outil de coupe. On utilise principalement deux techniques :
- tournage, pour les pièces de révolution (cylindres, cônes, sphères) : l’objet tourne et l'outil avance dans l'axe (chariotage) ou selon un rayon (dressage) ;
- fraisage : la pièce est bloquée et l'outil tourne et progresse dans la matière.
La difficulté de l'usinage tient à plusieurs paramètres :
- la limite élastique du métal, qu’il faut dépasser pour arracher la matière ;
- l'arrachement de matière provoque un écrouissage, donc un durcissement de la surface ; pour pouvoir enlever la « couche d’après », il faut donc « mordre » suffisamment dans la matière, cela définit la profondeur minimale entre deux passe, ou « copeau minimum » ;
- l'échauffement, donc la capacité de la pièce à résister à la température (chaleur massique, température de fusion) et sa capacité à évacuer la chaleur (conductivité thermique) ;
- les caractéristiques de l'outil (acier « rapide » ou carbure).
Ces paramètres déterminent la vitesse de rotation de la pièce (tournage) ou de l'outil (fraisage), la vitesse d'avancement de l'outil et la nécessité ou non de lubrifier.
Métal | Énergie (MJ/kg) |
---|---|
Aluminium et alliages | 3,8 à 5,6 |
Cuivre pur et alliages | 4,1 à 6,3 |
Acier | 5,6 à 9,8 |
Fonte | 3,6 à 5,7 |
Alliage de magnésium | 4,2 à 7,3 |
Nickel pur et alliages | 4,9 à 9,1 |
Titane pur et alliages | 6,6 à 8 |
Zinc et alliages | 4 à 5,5 |
L'usinage « conventionnel » ou « traditionnel » se fait sur une machine-outil (MO) commandée par un technicien qui effectue le montage de l'outil, la mise en place du brut et son maintien en position (bridage) et le réglage de la machine. Ce procédé est bien adapté pour les petites séries ou pour les retouches. Pour les grandes séries, on utilise des machines-outils à commande numérique (MOCN, ou simplement CN) programmée.
Un usinage soigné — technicien d'usinage qualifié avec une machine bien réglée, en usinage conventionnel — permet typiquement d'atteindre une précision « au centième » (1⁄100 mm = 10−5 m = 10 μm). Un usinage de précision permet de tenir des tolérances « au micron ».
Texture de fibres
[modifier | modifier le wikicode]

Outre l'écrouissage, le laminage, l'extrusion et l'estampage tendent à faire tourner les cristallites (monocristaux qui composent le métal). Du fait de la déformation, les grains sont allongés dans le sens de la déformation, mais ils ont aussi une direction cristalline préférentielle.
Prenons le cas de la traction simple. Nous avons vu que le glissement est un cisaillement entre des plans atomiques denses. On peut montrer que la sollicitation en cisaillement est maximale sur des plans faisant un angle de 45° avec la direction de traction : pour simplifier, un plan perpendiculaire à la traction a tendance à se faire « arracher » et non cisailler, et un plan parallèle à la traction se contente de s'étendre, c’est la position intermédiaire qui est la plus sollicitée en cisaillement (voir l'exercice Détermination du plan de scission maximal pour la traction simple). Les cristaux ne vont donc pas tous commencer à se cisailler en même temps : les cristallites ayant un plan dense faisant un angle proche de 45° avec la direction de traction vont se déformer en premier.
Ce faisant, les cristallites qui ne se déforment pas tournent, puisque l'alentour se déforme, et se commencent à se cisailler lorsqu'un de leur plan dense a une bonne orientation. Ainsi, pour des fortes déformations, la quasi totalité des cristallites sont orientés de sorte qu'un plan atomique dense fait un angle de 45° avec la direction de traction.
Cette orientation cristalline préférentielle est appelée « texture de fibre ». Cependant, ce terme est trompeur, car il pourrait faire croire que l’on a des « fils de cristaux ».
De fait, les propriétés mécaniques, en particulier la limite élastique et la ductilité, dépendent de la direction dans laquelle on sollicite l’objet : le matériau est « anisotrope » (non-isotrope).
Certains traitements thermiques provoquent une recristallisation, c'est-à-dire réorganisation des atomes pour former des nouveaux cristaux. On a alors une structure équiaxe, sans direction préférentielle.
Voir aussi
[modifier | modifier le wikicode]- Introduction à la science des matériaux/Les métaux
- Métallurgie primaire
- Philibert et col. (1998) p. 18-39
- formage
- Barralis et Maeder (1991) p. 10, 141-143
- Philibert et col. (1998) p. 798, 805, 833-862
Notes
[modifier | modifier le wikicode]- ↑ P. Dal Zotto, J.-M. Larre, A. Merlet, L. Picau, Mémotech génie énergétique, Paris, Casteilla, 1996 (ISBN 978-2-206-10018-0), p. 13 , lien Sudoc et pages de Wikipédia pour les différents matériaux
- ↑ Inconel est une marque déposée par Special Metals Corporation
- ↑ pièce ayant la forme d'un cylindre creux dans laquelle vient se placer un axe, un arbre, et assurant le guidage en rotation
- ↑ pour l'eau froide
- ↑ 5,0 et 5,1 logiciel CES EduPack 2007, Granta Design Limited http://www.grantadesign.com/